Locating Ground-Faults for a Safer Rail System
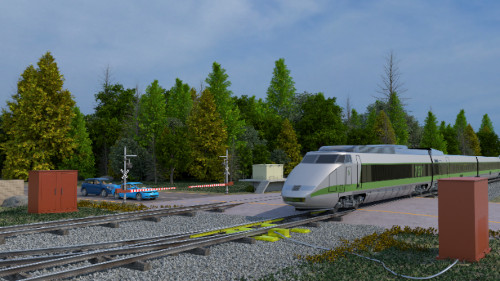
Railways require safe, reliable power systems to support signals, track heaters, switching points, and communication infrastructure for both rolling stock and rail cars. Trackside equipment must also be protected from failure, and with thousands of miles of track to maintain, rail operators demand maximum visibility to assess information regarding the health and condition of its infrastructure in real time. US rail transit systems are subject to harsh operating conditions and incidents of theft, accidental damage, and degradation. Finding and locating faults is challenging, often requiring rail personnel to spend thousands of hours along the track inspecting and locating failing cable. Because of this, rail personnel are constantly seeking more efficient ways to locate faults and in turn, save valuable time and money.
What is the benefit to finding faults early?
The benefit of effective fault finding translates into fewer train delays and improved customer service with reduced associated costs for rail operators. More than 50% of rail signaling power supply issues result from ground-faults where damage or deterioration of a cable or its insulating covering will eventually lead to failure, impacting the safety and efficiency of rail operations. Since rail signaling systems are typically ungrounded, a faulted circuit could change the state of a signal or trigger the shutdown of the train. On ungrounded systems, the first ground fault can typically go undetected for days or months, or worse, until a devastating second ground fault occurs while the first fault remains. Critical faults that emerge at lower intervention/insulation limits are even more difficult to track and pinpoint, and therefore present a greater challenge.
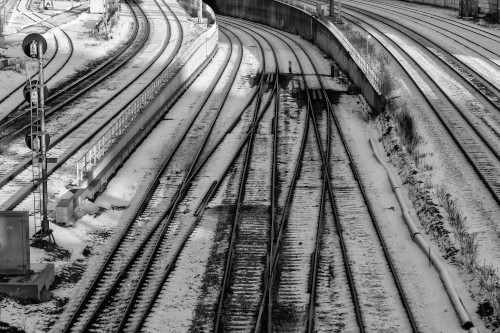
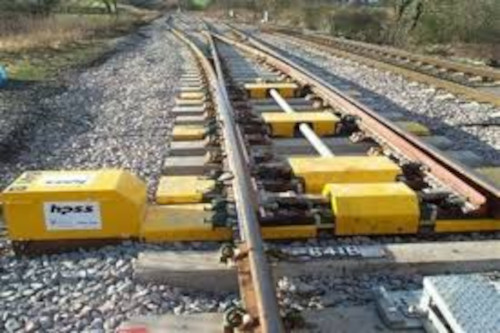
It is important to note that the rail electrical standards of the American Public Transportation Association (APTA), require ground detection, inspection and maintenance procedures for AC and DC rail power systems. Detecting ground faults on the ungrounded signal power system has historically been accomplished using instruments physically carried out along the tracks by maintenance crews at regularly scheduled maintenance intervals, taking current and voltage measurements and calculating leakage currents. This requires many hours to cover the thousands of miles of signal power that exist in each operator’s system and does not enable timely fault detection
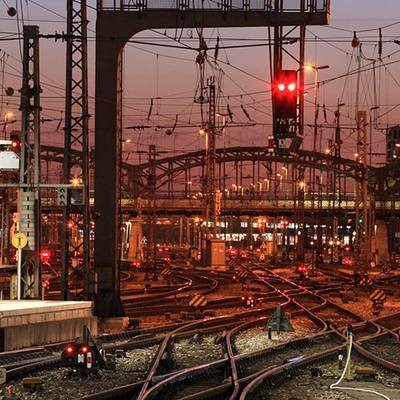
The Bender solution
By employing a Bender predictive insulation monitoring system means that as leakage current increases and/or insulation resistance decreases, a ground fault is caused and will then trigger an alarm and fault location pulse. Bender’s Predictive Rail fault location system (EDS) will identify and locate these pulses in real time as ground faults at the actual location on the rail signaling power network. Bender Insulation monitoring systems can also identify less critical emerging faults at lower intervention/insulation limits which are more difficult to track and pinpoint. This allows for earlier detection and planned maintenance versus unplanned outages due to signal power interruptions caused by ground faults.
Where Bender’s Rail Insulation Monitoring systems have been adopted as the principal method of tracking and locating faults on the rail signaling power network, rail transit systems are able to detect and locate faults in real time due to the active and predictive capabilities embedded in Bender’s ISO insulation monitors and EDS fault locators.
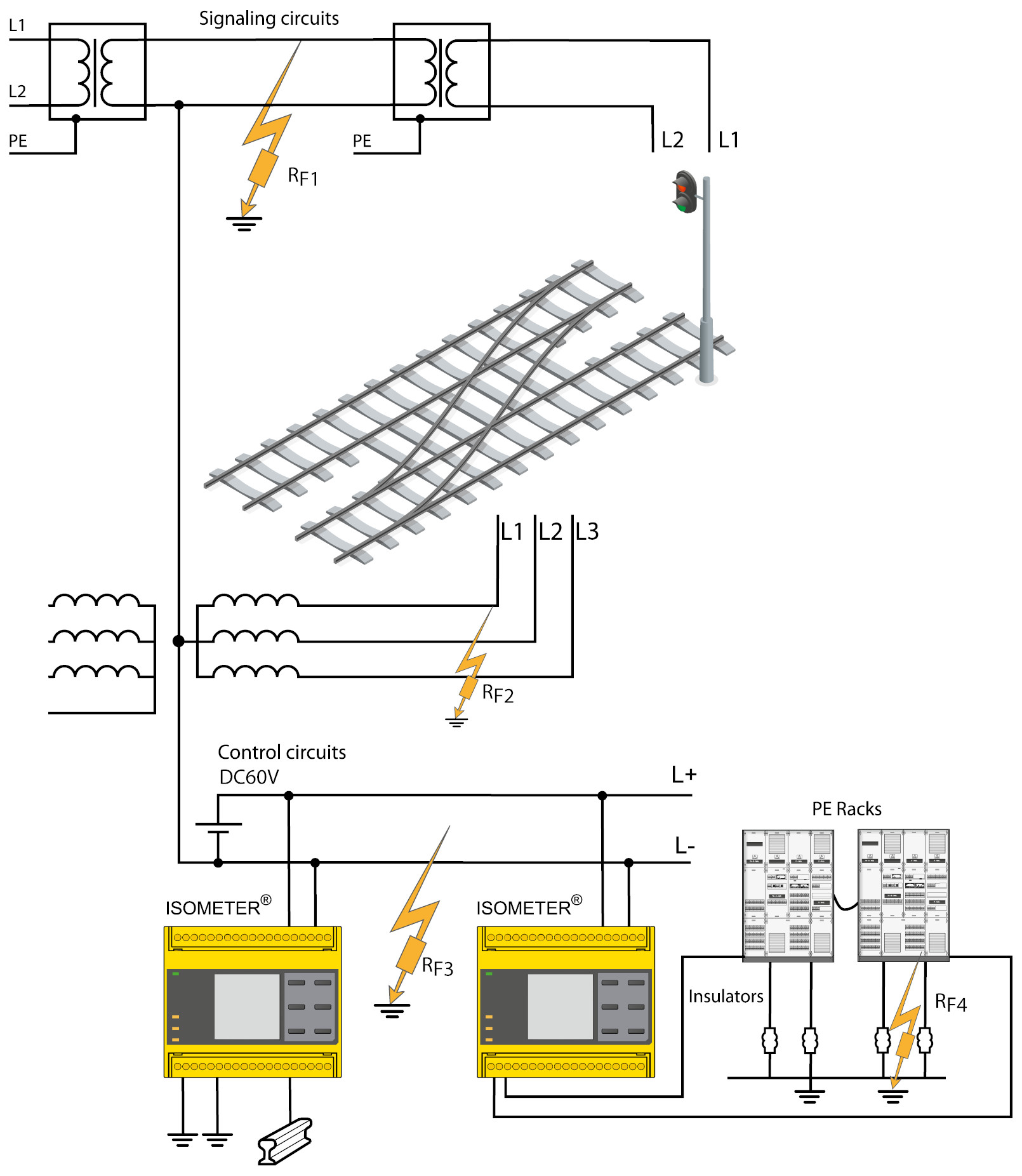
For more information about this application or to learn more about Bender technology related to your specific application, contact our team of experts.
This article is for informational purposes only. Bender provides the information "as is" without warranty and is not responsible for its accuracy or reliability. No warranties are given regarding its suitability for any specific circumstances.