Case Study: Advanced Ground Fault Monitoring in Generating Stations
Power generation has been an integral industry that generates electricity to be distributed to all sectors of activity, both residential and industrial. It uses many sources of energy to generate electricity: water, wind, solar, nuclear, fossil fuels, and more. Many of these energy sources are called "prime movers", which means a mechanical input is involved. For example, the gravity of water helps move turbine propellers. Depending on the configuration of generators, they may also require a DC field source to "excite" the rotor windings of the generators. This field source is often referred as the exciter or excitation system.
Exciter Systems Need protection
There are many configurations for exciter systems, and they are often categorized as static excitation or dynamic excitation. These DC sources are often sourced by step-down transformers from the main stator system.
Rotor windings are highly-stressed components in modern electric generators, as the rotor itself is the rotating part of the generator or alternator. Their insulation degrades over time via their dielectric elements. If a rotor needs to be replaced, the labor costs, unexpected downtime, and revenue losses all make significant financial deterrents of letting the rotor fail.
Hydro-Generation Companies Measure Degradation of Rotor Insulation
The companies that construct and manage hydroelectric generating stations need to measure the insulation resistance of the exciter systems and detect when the rotor insulation has degraded past a certain point. These companies often refer to this insulation measurement as "field ground relays". These hydro companies have independently tested many suppliers, and their results have shown that Bender's ISOMETER® Insulation Monitoring Device (IMD) is the most accurate and reliable field ground relay on the market. For many years now, this industry has mandated all exciter systems to be equipped by the ISOMETER IRDH series, and more recently the iso685.
The IMD measures the insulation resistance of the whole exciter system, from the step-down transformer, through the AC/DC rectifier bridge and all the way to the rotor windings. The wide range of measurement allows hydro-generation companies to monitor the insulation resistance in the hundreds of kΩ and even MΩ, while maximizing the generator production uptime to its very limit by selecting two alarm setpoints of 40 kΩ and 10 kΩ, for example. Once the insulation drops below the second alarm threshold, it signifies to the maintenance team to plan a shutdown to clean the rotor.
DC Auxiliary Distributions in Generating Stations
Going one step further, a hydro-generating company had facilities that needed an upgrade for its low voltage DC distribution systems. Thanks to the company's experience with Bender regarding exciter systems, they asked for Bender’s advice. The older technology did not permit this company to locate faults after ground faults occurred in their systems. They wanted to make the future DC switchgears smarter and to make life easier for their maintenance team. In many cases, the fault remained unresolved because the loads on the DC distributions are critical to maintain operation in the generating station, and therefore the "switch-off and check" approach on each feeder wouldn’t work.
The Bender team worked with the project consultant and system integrator to fit in the fault location system of iso685-x-P along with EDS440 fault locating monitor in a 250V auxiliary distribution. The same principle of insulation monitoring from the iso685 series allows for reliable detection of ground faults. Once that happens, the iso685-x-P monitor switches from IMD mode to EDS mode, in which a different signal is sent throughout the DC distribution. The EDS440 and its connected current transformers would pick up that signal only on the faulted feeder and associated CT. Up to 12 CT’s can be connected to a single EDS440 relay and in turn, the EDS440 will automatically determine which feeder has the detected ground fault. With this implementation of Bender ground fault detection and location technology, the hydro-generating company can help its maintenance team quickly locate ground faults. On-site commissioning and training have also contributed greatly to support this customer in familiarizing them with Bender technology.
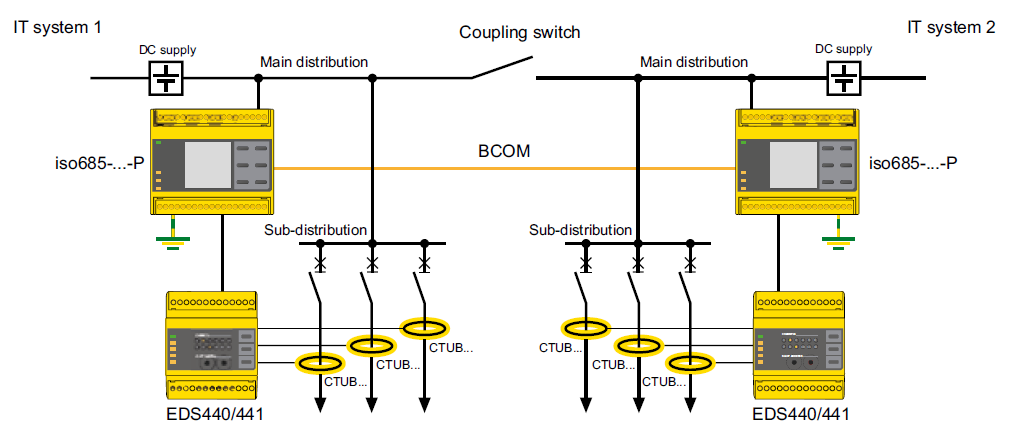
Conclusion
Hydro-generation facilities need the best technology when it comes to electrical safety protection. This is why Bender has developed and maintained the best in class of insulation monitoring technology. Hydro-generation customers and their consultants were very pleased with Bender's IMD products that provided such an advanced level of protection for their exciter systems and DC auxiliary distributions.
For more information about this application or to learn more about Bender technology related to your specific application, contact our team of experts.
This article is for informational purposes only. Bender provides the information "as is" without warranty and is not responsible for its accuracy or reliability. No warranties are given regarding its suitability for any specific circumstances.