Ground-Fault Protection and Location in Pulp and Paper Mills
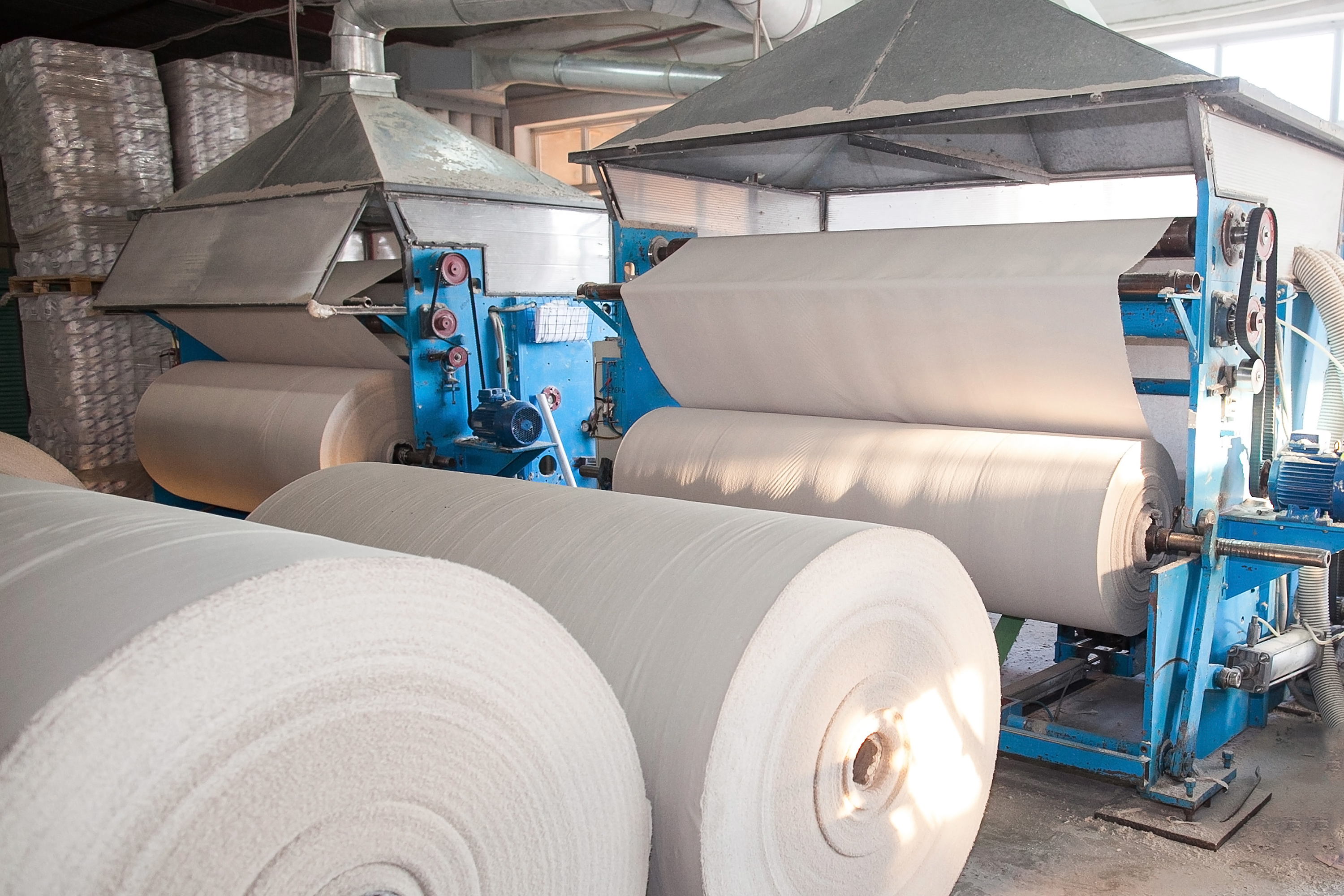
Historically, the paper industry has always been an early adopter of new technology. For example, the addition of advanced drives and controls have allowed paper manufacturing machines to produce reliable and quality product more efficiently. High Resistance Grounding is another example and is widely used throughout the industry. However, the process from wood yard to final product is often spread over a large area, making the task of locating faults on these systems time consuming and difficult. Interruption of the process, in particular, interruption to the paper machines that produce large rolls of product at high speed, is expensive and therefore very undesirable. Any type of unplanned interruption, whether from drive or control circuit trips, can have a painful impact on operations.
Riiiippppp!Ripping paper can be gratifying when you are crumpling it up and throwing it in a waste basket. It is not gratifying to see it happen on a paper machine. The process of rewinding or threading the paper to get the process started can be very labor intensive and can waste a tremendous amount of product.
To help prevent issues on the drives and prevent the control circuits from stopping production, ground-fault protection is alarm only. Historically, this was done as an ungrounded or delta 3-phase power source. In the event of a single phase-to-ground fault, operators would continue to run the paper machine and make necessary repairs or troubleshoot issues (stemming from the ground fault) at a convenient time. Repairs could be started at the end of a shift or another day when there are additional electricians or engineers available – and not at 2 am when the fault may have first appeared. This practice of leaving the fault on the system for an extended period of time is a trap that many facilities fall into.
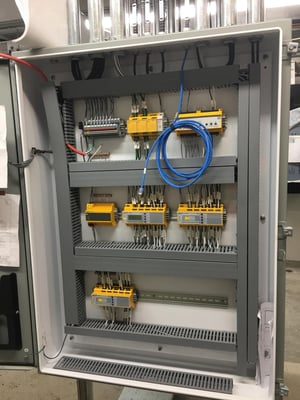
Multiple ways to save
The investment to install an HRG package with fault location is easy to justify. After installation of a Bender HRG system, users will benefit from a safer and more automated system. Most older locations will have a record of the cost of each unscheduled downtime that was caused by electrical faults. If 80 to 95% of the electrical faults start as a ground fault, you can use an average cost x .8 for a conservative estimate. The automation of ground-fault location allows electricians more time to correct problems instead of searching for faults. Operations can set time limits for running with a fault on a system to avoid the pitfall of ignoring the alarm. If ignored for long enough, a second fault could occur, and the costs of phase-to-phase faults can be much higher than single-phase faults. Due to the additional energy released, they often result in more expensive motor rewinds and more cleanup in the switchgear.
Savings comes from the following areas:
- Reduction of unscheduled maintenance
- Reduction of time for ground-fault location
- Reduction of time for repairs
- Reduction of severity of repairs
- Enhanced safety
The hardest to quantify is the cost savings that result in the improved safety. Electrical incidents and fatalities can cost companies millions. While this article has primarily covered paper machines, the use of electricity in other parts of the operation are just as critical. Pumps and electrically-operated valves are used on the boilers, and interruption or problems in those areas can be catastrophic and dangerous due to the high-pressure steam. To enhance reliability further on high resistance grounded systems, use a neutral grounding resistor monitoring relay such as the NGRM500 that will indicate the condition of the ground-path resistance. Ground-fault protection that uses current sensors requires a continuous path back to the source transformer or generator.
Plant wide HRG and fault location can be implemented to help prevent downtime. It can include the Medium Voltage (4160 and 2400 V) sections as well as the low voltage (480 or 600 V). Older HRG systems typically implement a simple pulsing grounding resistor system with analog gauges to indicate voltage current of the resistor and they typically use a clamp-style ammeter to locate the pulsing current of the fault. This requires opening compartments and exposing electricians to electrical hazards. The benefit of an automated HRG system can easily be achieved by installing fixed equipment in breaker sections or motor control centers. The more ground-fault detectors are added, the more specific the automated fault location can be. Bender has developed multichannel ground-fault devices to make this more economical. RCMS460 and RCMS490 can monitor 12 channels per relay and they are widely used in larger systems.
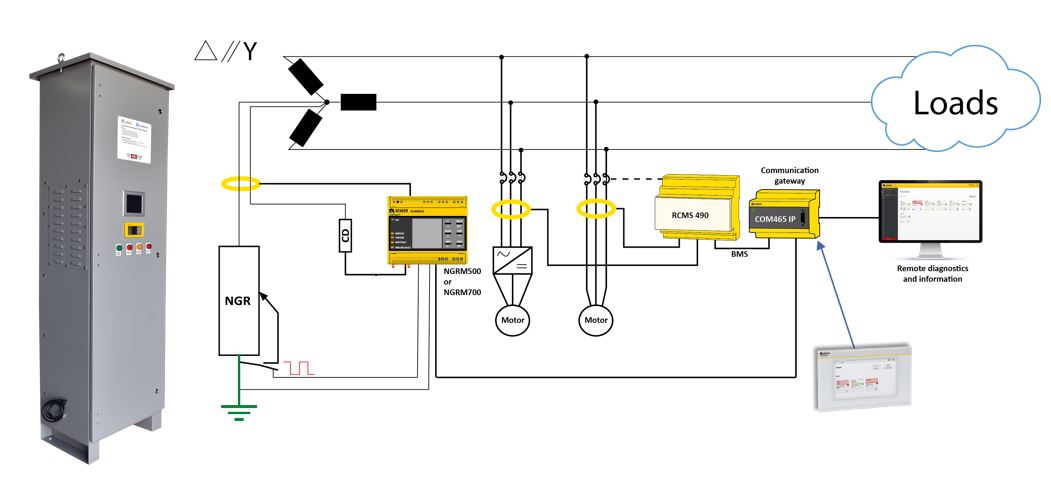
Trending for prevention
Often, a combination of different grounding methods appear in the same system. Bender has both products and knowledge in all methods, as well as the ability to assist customers in getting more value out of their real-time trended information. Knowing the state of an ungrounded system's insulation or a grounded system's leakage current can be used to better predict where preventative maintenance on equipment may be required.
For more information about this application or to learn more about Bender technology related to your specific application, contact our team of experts.
This article is for informational purposes only. Bender provides the information "as is" without warranty and is not responsible for its accuracy or reliability. No warranties are given regarding its suitability for any specific circumstances.