Case Study: Mining Company Vulcan Materials Partners with Bender
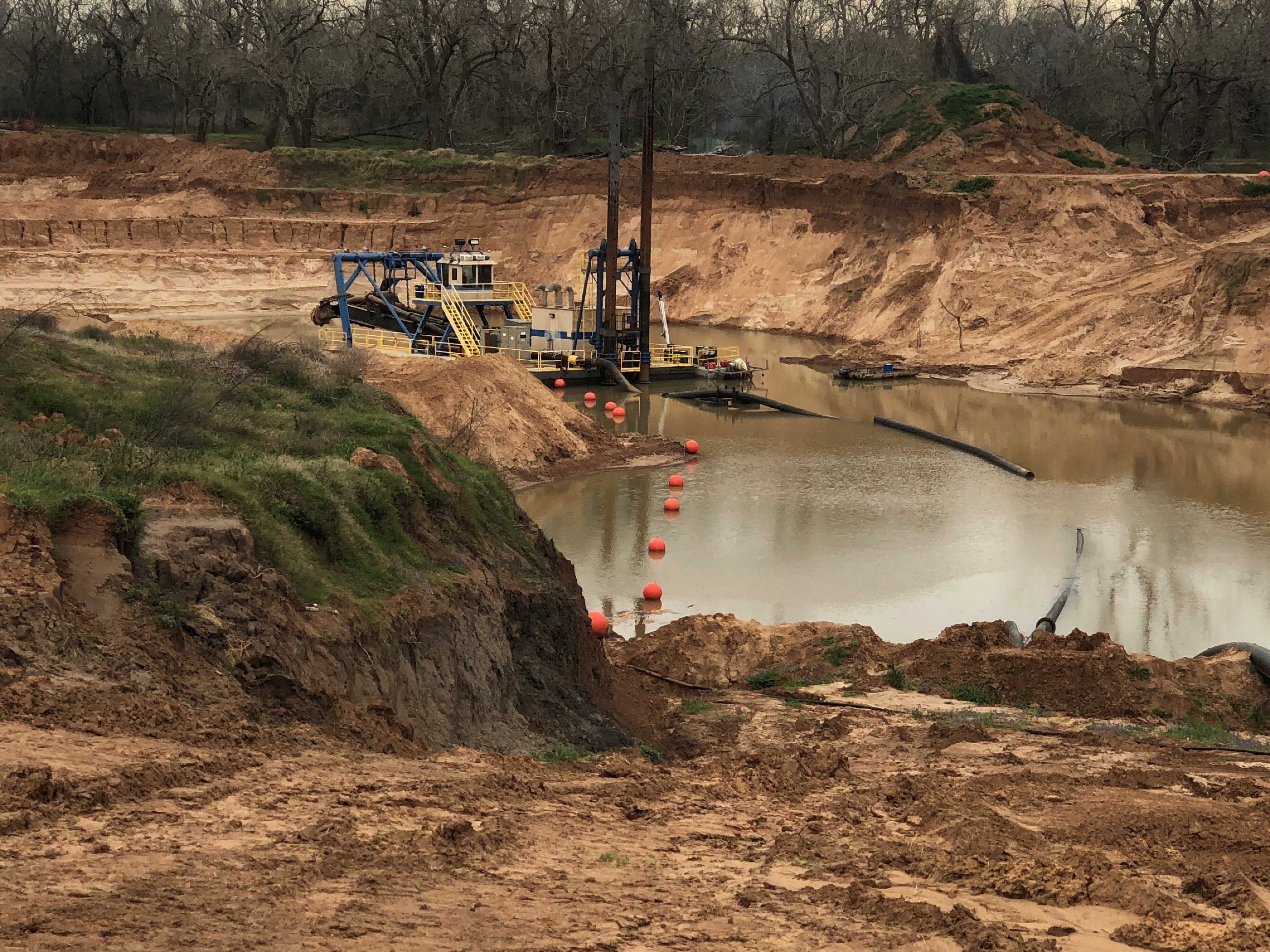
Mines can be one of the harshest environments to operate in since equipment is often installed in remote locations where the ore or material being extracted is found in large deposits. The equipment is frequently mounted outdoors and is exposed to the elements. Because of this, miners know they need quality equipment if they want it to last.
The supply of construction materials is one of the primary focuses of Bender’s customer solutions. Vulcan Materials Company is the nation’s largest producer of construction aggregates—primarily crushed stone, sand, and gravel—and a major producer of aggregates-based construction materials, including asphalt and ready-mixed concrete. Their coast-to-coast footprint and strategic distribution network align with and serve the nation’s growth centers. Recently, Bender partnered with Vulcan to provide solutions for their mining environments. This partnership provides operators with reliable equipment that can deliver information on the status of the operation. This enables an improved uptime and operational efficiency.
What systems are typically used in mines?
Global mining customers have been using resistance grounding on portable and fixed applications in medium-voltage and low-voltage substations for many years. The control of ground-fault current and the capability to restrict the touch potential on portable loads are primary reasons for the implementation of resistance grounding in the mining industry. In refining and processing areas, alarm-only systems are often selected for their ability to improve continuity of service. Bender offers grounding systems and relays including ground-fault and neutral-grounding resistor monitors and ground-continuity monitoring devices.
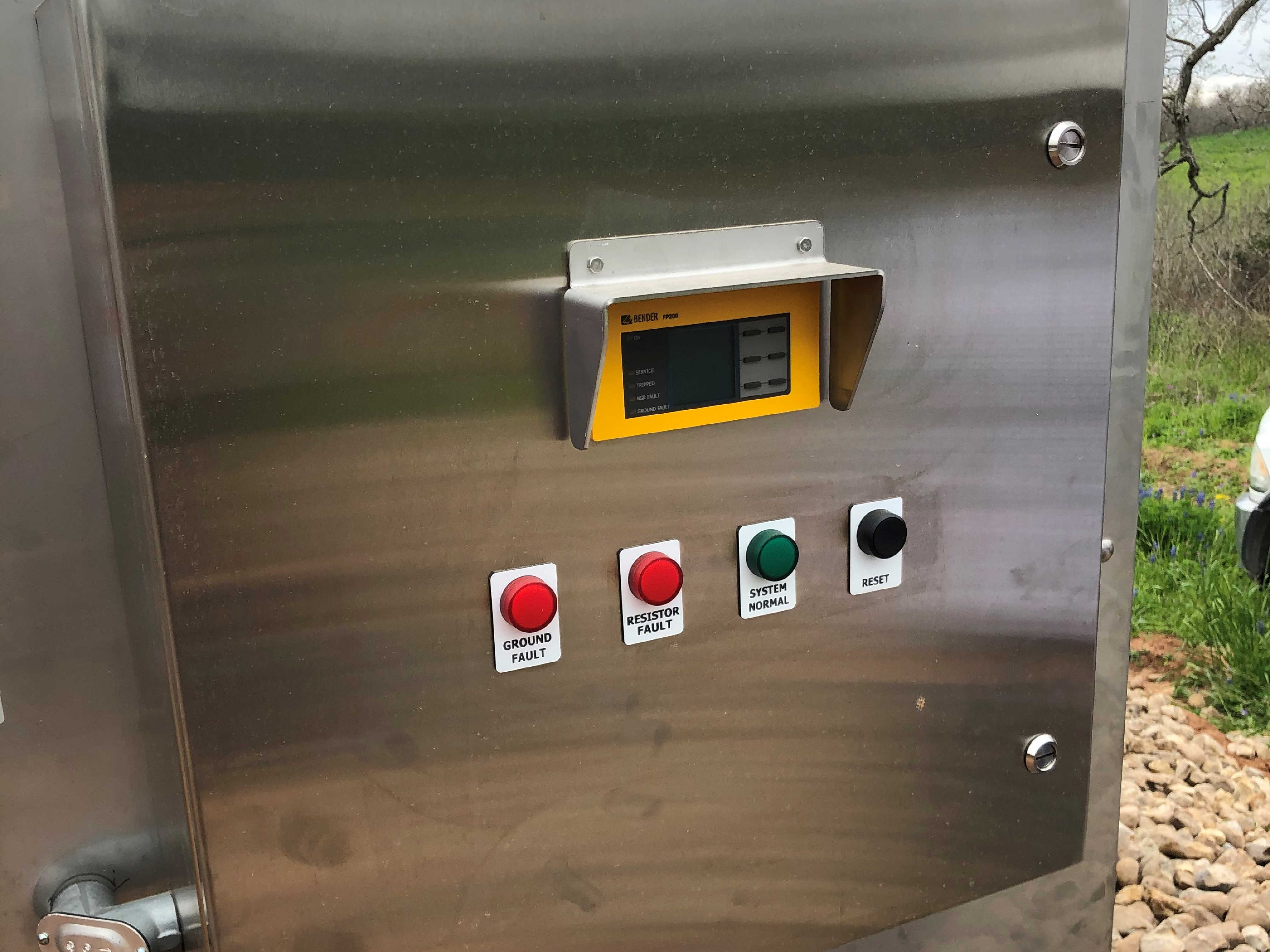
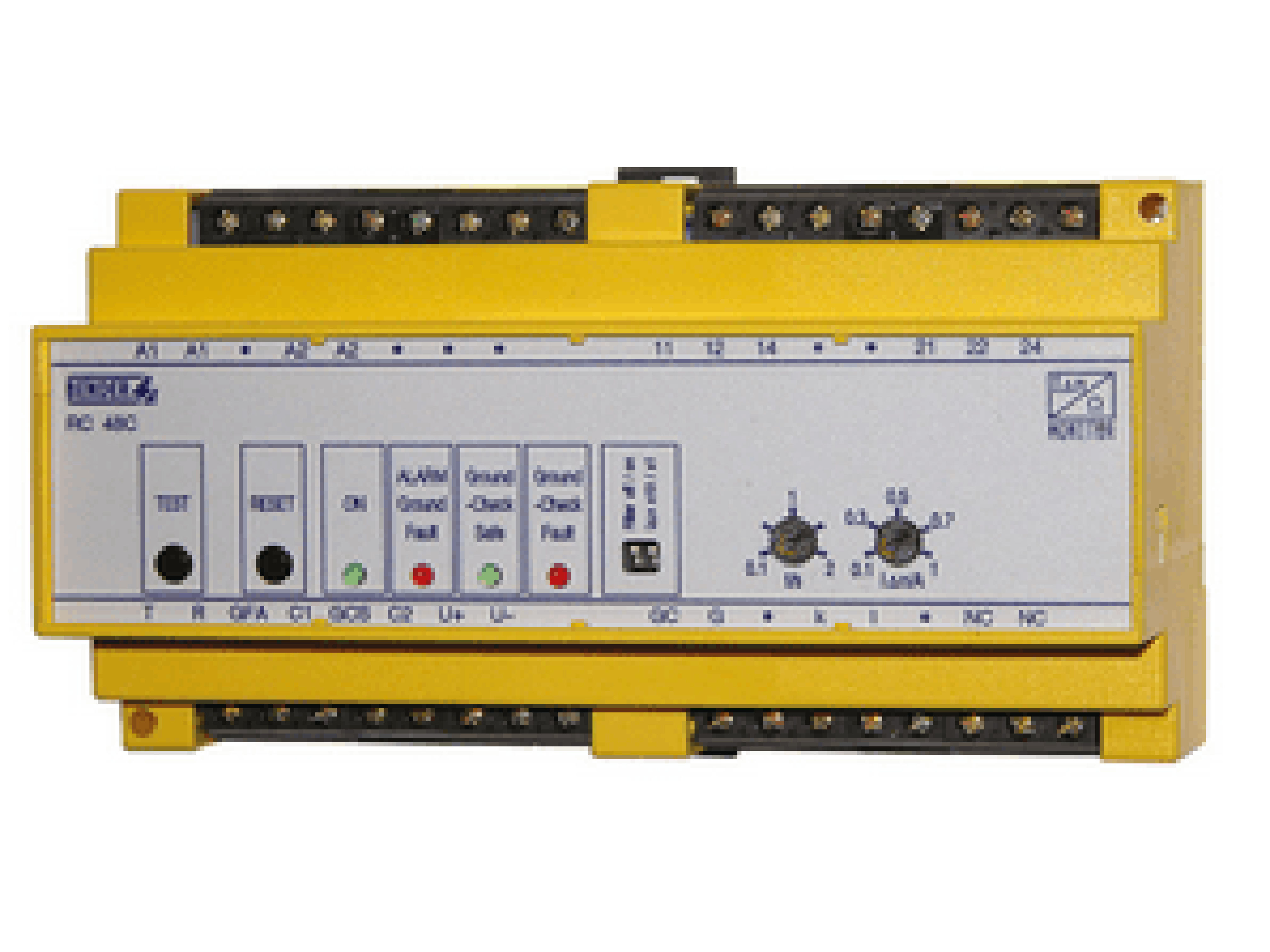
The enclosure below was installed at a Vulcan sand and gravel plant in Texas and is an all-in-one solution that helps protect the critical grounding resistor.
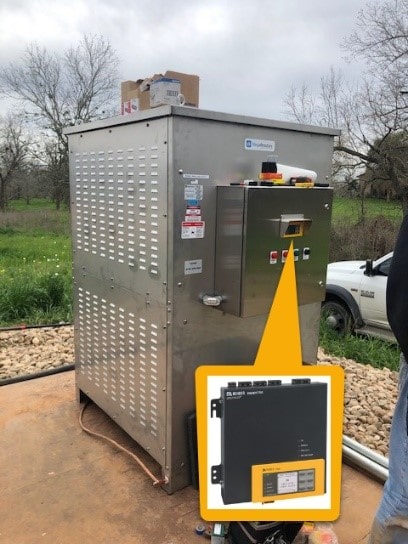
The importance of the grounding resistor
Without the resistor, the system’s ground-fault protection capability would fail to function and system operation would be unsafe. The smaller enclosure on the side of the NGR houses the control equipment, including one of Bender’s NGRM series of advanced NGR monitoring relays. After initial design reviews, Vulcan Materials has specified Bender Grounding solutions for their mining needs.
Integrated product solutions that communicate site conditions (locally and remotely) can provide timely information for remote staff and provide enhanced safety at remote sites.
"The Bender MV HRG/NGR recently installed at our Dredge Site near Simonton, Texas has already revealed its value in identification of leakage currents within the power delivery system to the Dredge. Easily accessed stored data is available to our electricians, in turn significantly enhancing effective troubleshooting and mitigating losses due to plant down-time."
- Andy Anderson, PE Principal Electrical Engineer
A final Bender advantage is enhanced protection of non-linear loads such as adjustable frequency drives (AFDs, VFDs, ASDs) used on equipment such as submersible pumps and conveyors. The Mine Safety and Health Administration (MSHA) has been aware of the inadequacies of using 60 Hz relays on such drive applications and has been promoting the application of such full frequency capable protection relays for many years.
For more information about this application or to learn more about Bender technology related to your specific application, contact our team of experts.
This article is for informational purposes only. Bender provides the information "as is" without warranty and is not responsible for its accuracy or reliability. No warranties are given regarding its suitability for any specific circumstances.