Case Study: Safer Cement Production with Bender
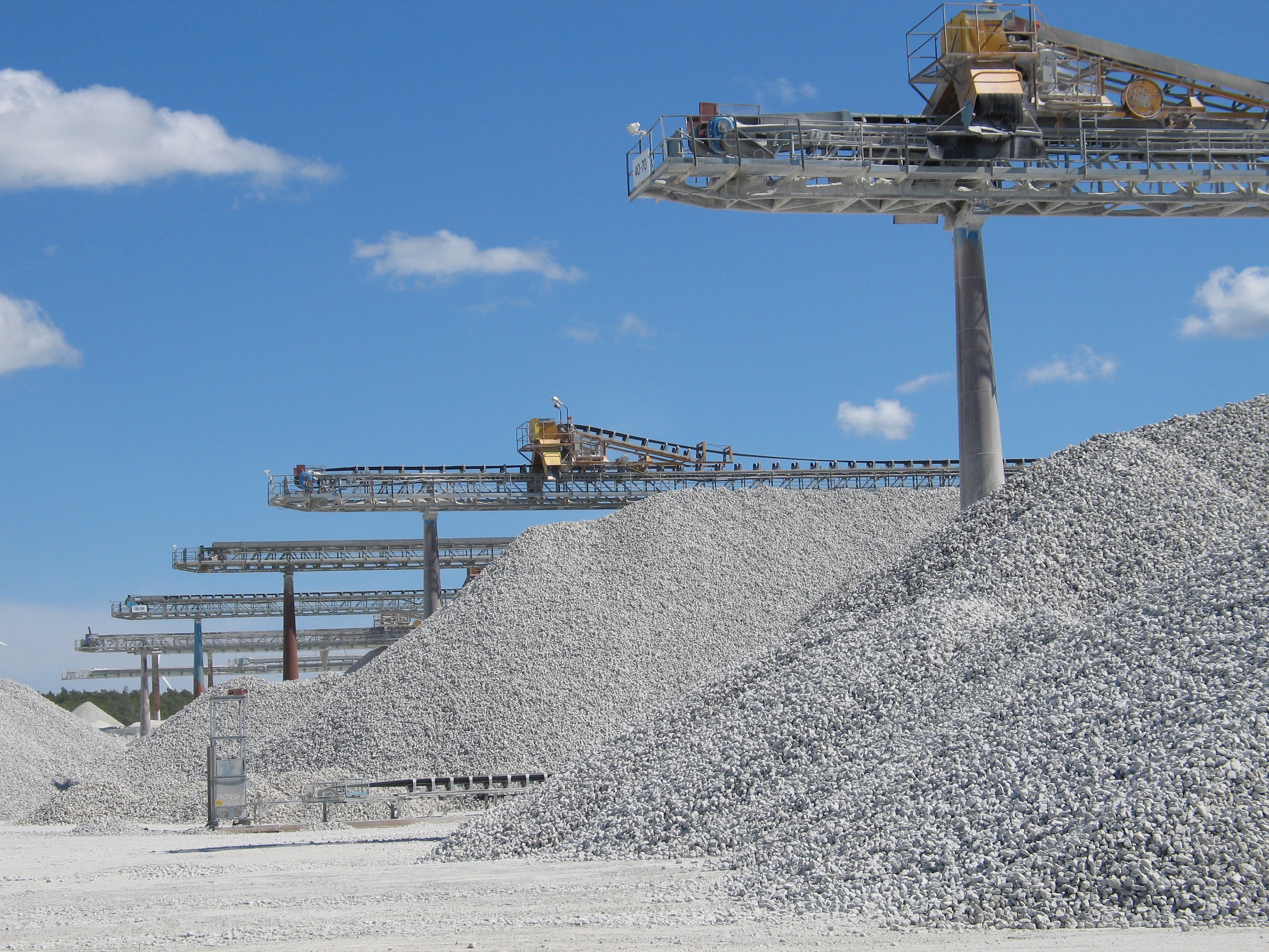
Cement production is a complex and energy-intensive process. In order to ensure high quality, the freshly-fired cement must be cooled down very precisely. An ungrounded power supply system is used to detect faults in the cooling system at an early stage and to avoid failures. This is monitored with insulation measurement technology from Bender, which you can explore in more detail in this application video.
Solutions for the cement industry
Elettronica Santerno S.p.A. is a company based in Italy and has been part of the Enertronica Group since 2016. The company, which develops converters and motor starters for industrial applications and renewable energies, has been present in the world market for 40 years. They offer a wide range of products and solutions for cement production, such as high-performance conveyor belts, crushers, kilns, ventilation systems, and other products and services.
Speed and air flow must be right
The cement production process begins in a quarry. The material obtained is transported to a crushing plant where it is crushed into gravel. The raw gravel is transported via conveyor belts or rail vehicles to a cement plant before being stored in a mixed-bed silo and homogenized. The raw material is then ground into raw meal in mills driven by powerful electric motors and deacidified. In a kiln of around 1,450 degrees, the meal is burned into a cement clinker, which is then cooled and ground. The resulting cement is processed with water and additives to make concrete that is mainly used in the construction of buildings.
Quality requires precision
In several production steps such as crushing, separation, and cooling, controlling the speed has a major impact on the quality of the material produced and on operational efficiency. Particularly during the cooling process, the precise control of the fan speed and the resulting airflow significantly contributes to the energy efficiency of the plant.
The application for a cement plant located in northern Italy has four radial fans at the kiln outlet to cool the cement clinker. These are powered by regenerative frequency converters. This enables the kinetic energy produced during the braking phase, when the motor is turned into a generator, to be fed back into the main supply as electrical energy.
The frequency converters are each supplied by a transformer that converts the voltage from 6 kV to 690 V. The windings are primarily and secondarily wired in a triangle and set up as an ungrounded system. The four Sinus Penta frequency converters have an output of 1 MW to drive the radial fans, which in turn have an output of 1 MW at 3 x 690 VAC/50 Hz.
Monitoring with Bender
After a detailed technical consultation, the company decided to use four iso685-S-FP200 insulation monitoring devices connected to a 3AC 690 V mains supply. These devices monitor the insulation resistance of the frequency inverters and motors at frequencies of < 10 Hz. For Santerno, not only does this mean fast fault detection but also ensuring a 24-hour operation and the ability to prevent cost-intensive, unscheduled maintenance downtime.
If an insulation value falls below a set value, an alarm is signaled via an output relay. The converter also uses a digital input to inform the insulation monitoring device whether a motor is running or at a standstill. A Profibus communication has also been established between the insulation monitoring devices and a central control system. This enables remote diagnosis of the entire system, thus ensuring availability 365 days a year.
The FP200 display installed in the converter control cabinet door not only displays the alarms, but also the insulation values. These can be displayed both numerically and graphically and thus provide ease of use to the operator and service personnel.
Have a need for a similar solution? Bender can help!
Please do not hesitate to engage Bender in your design discussions, our team of application engineers and regional-based resources have extensive experience in applying and supporting insulation monitoring and ground-fault monitoring for your DC-coupled systems.
For more information about this application or to learn more about Bender technology related to your specific application, contact our team of experts.
This article is for informational purposes only. Bender provides the information "as is" without warranty and is not responsible for its accuracy or reliability. No warranties are given regarding its suitability for any specific circumstances.